Semi- Finalist (Top 20) - Terra Carta Design Lab, Sustainable Market Initiative, Royal College of Art London(UK)
Graduation Project at Design Science Lab
Mentors - Sweety TAUR, Sahil THAPPA
Fres-o-lar is a project developed to promote sustainable energy consumption in metal casting for Dhokra artisans. It features a large polycarbonate Fresnel lens with a solar tracker to concentrate solar energy, transforming it into heat for melting metal while giving up to 95% energy efficiency. This innovation replaces the reliance on fossil fuels with clean, Renewable energy aims to provide an environmentally conscious solution for metal recycling and reducing greenhouse gas emissions in the process.
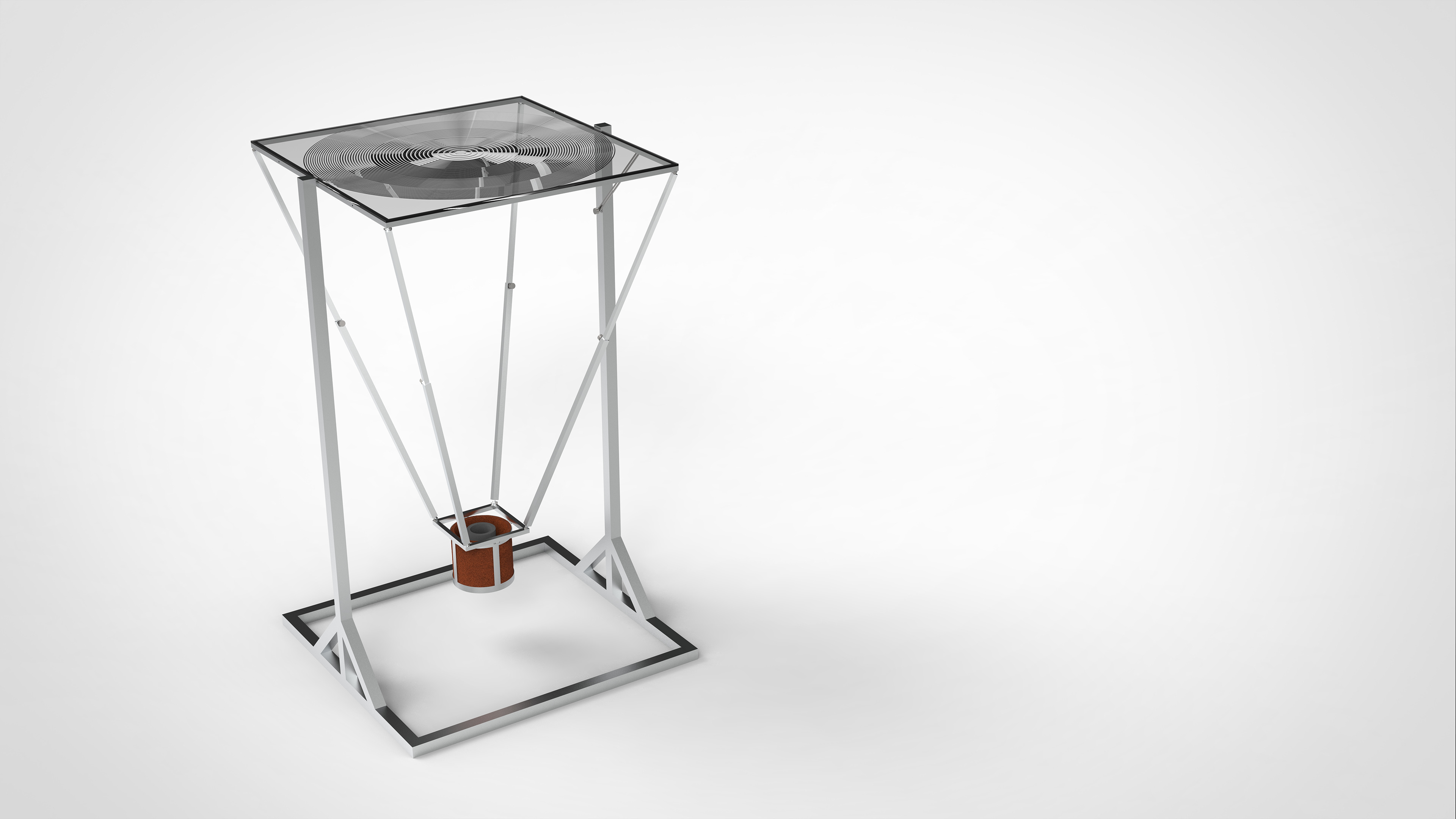
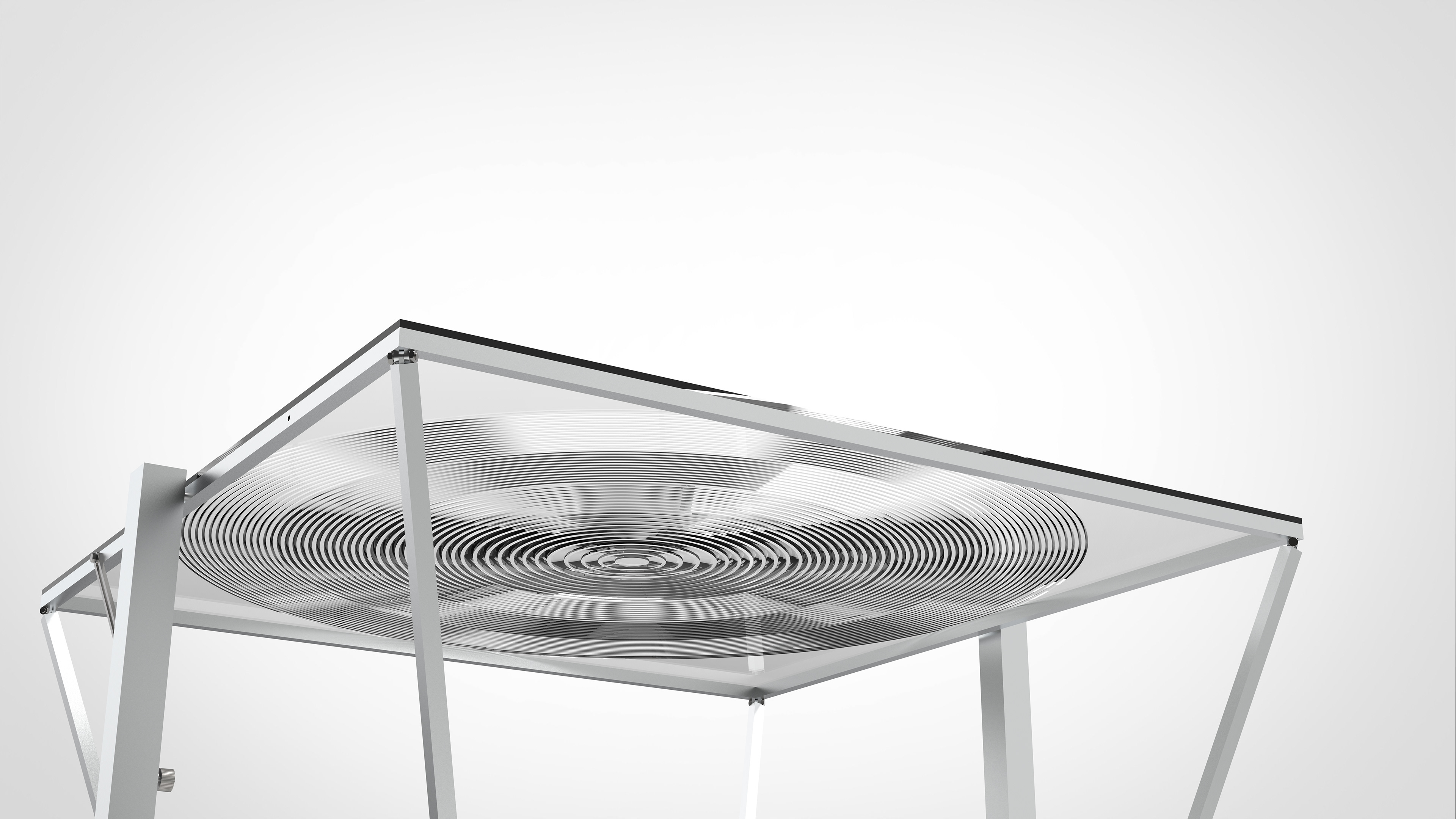
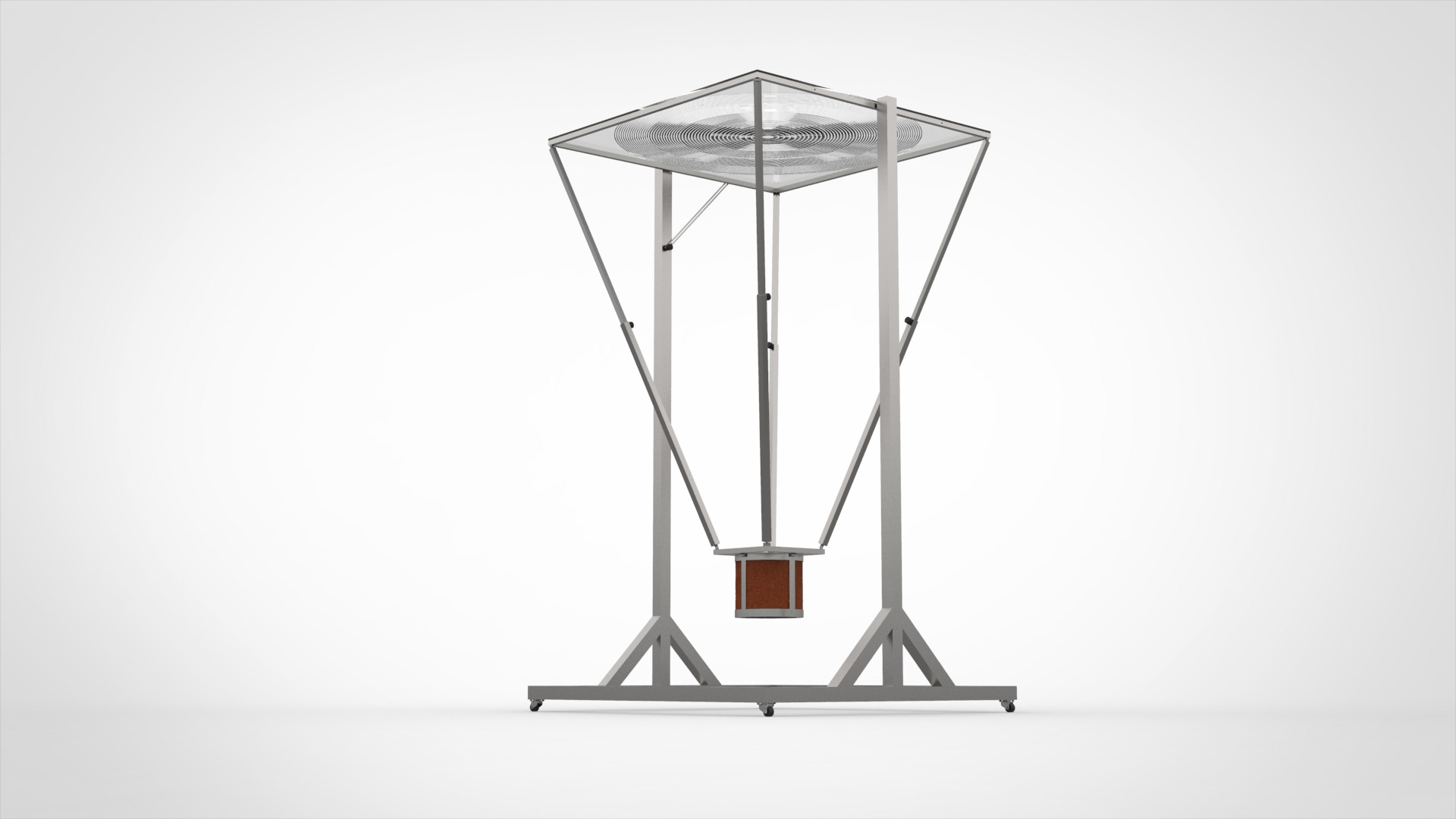
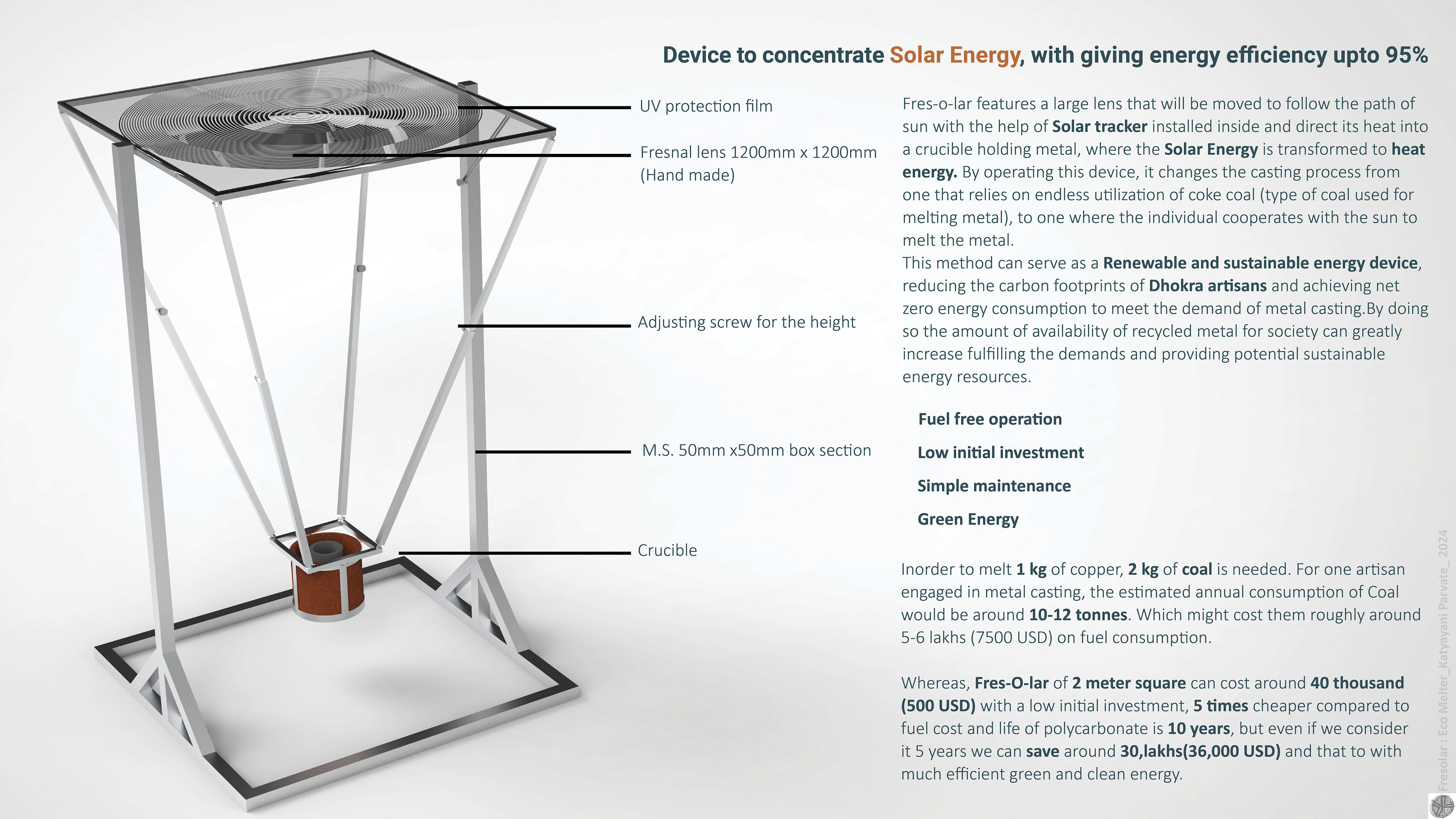
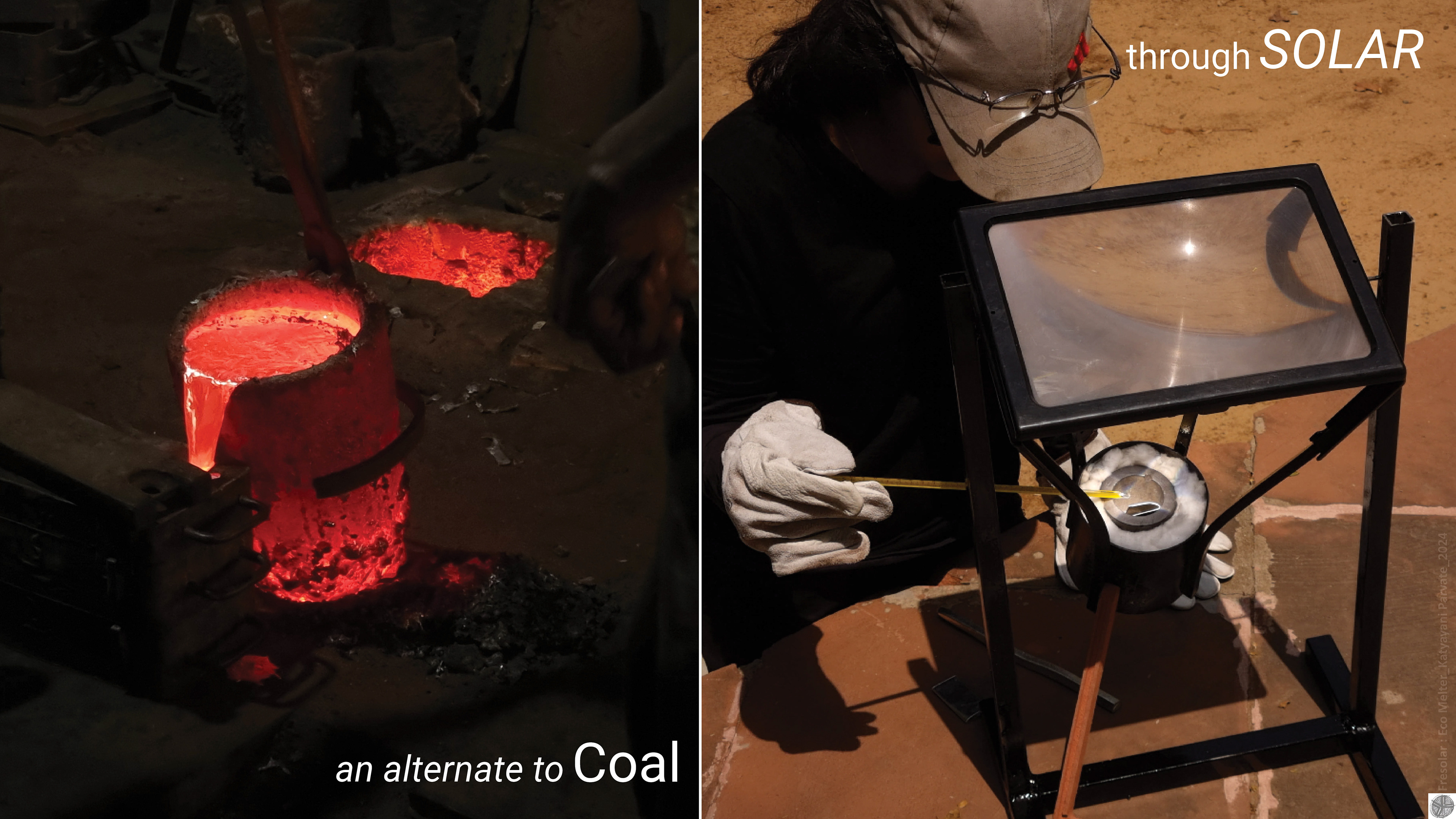
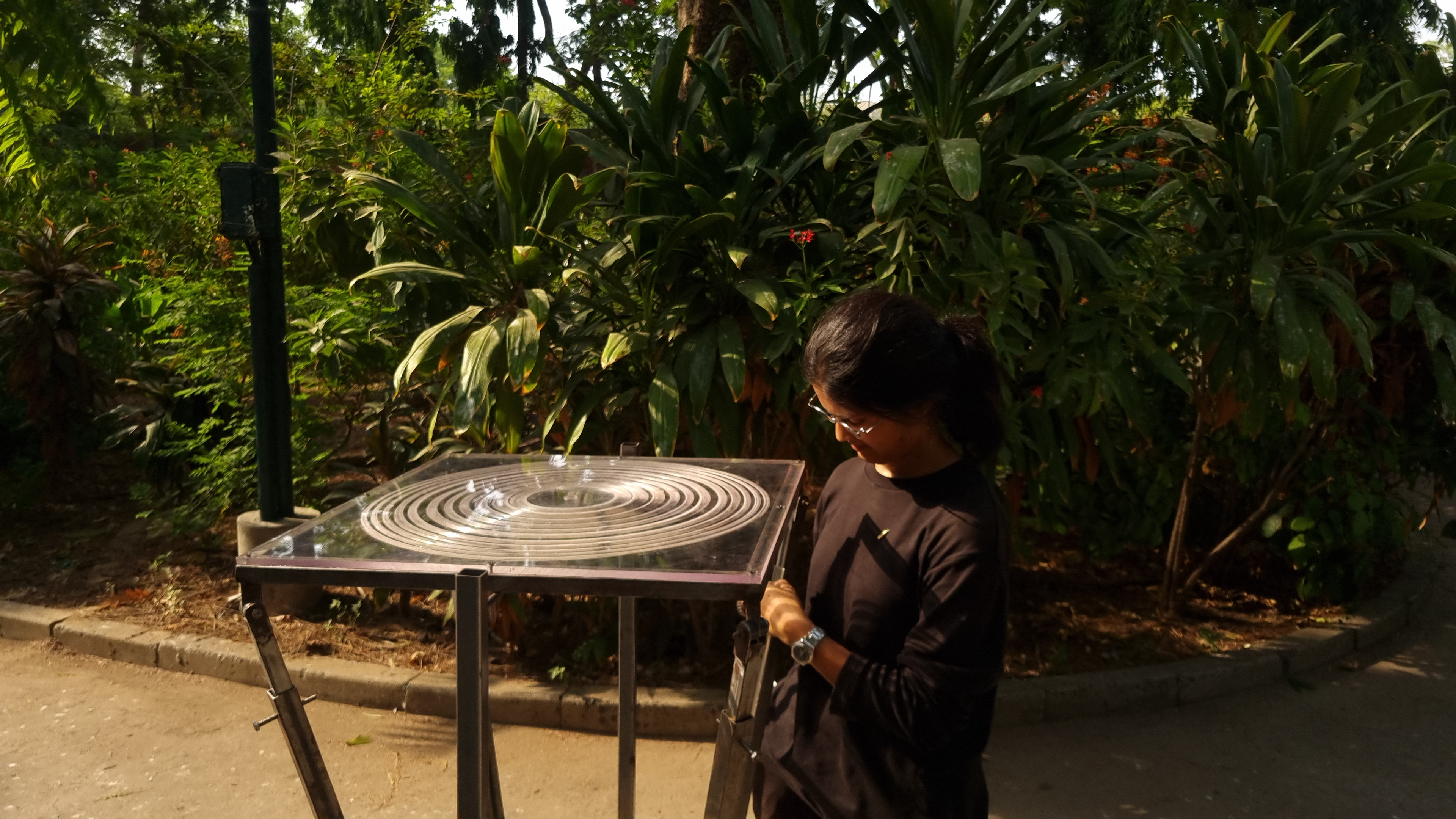
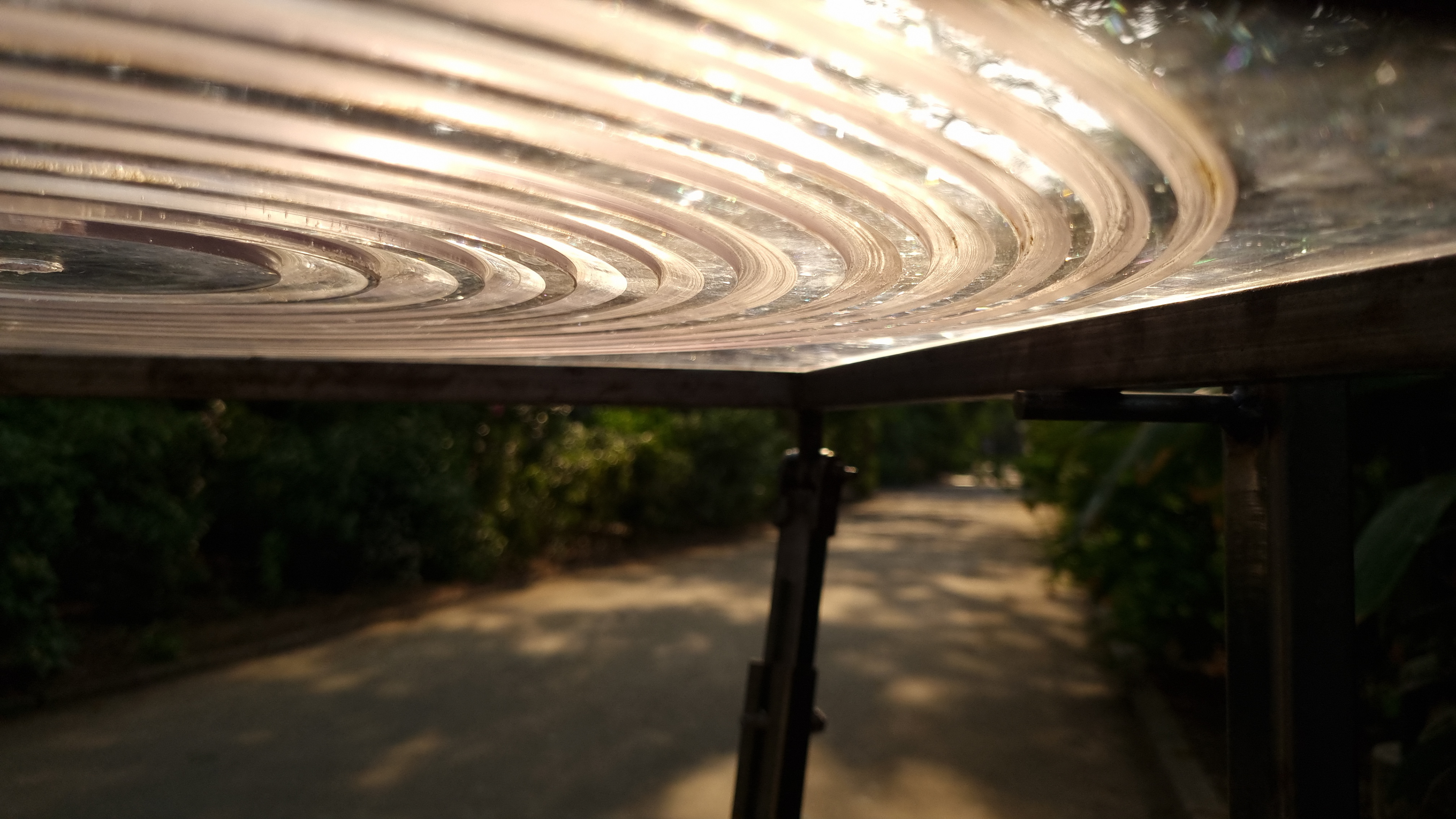
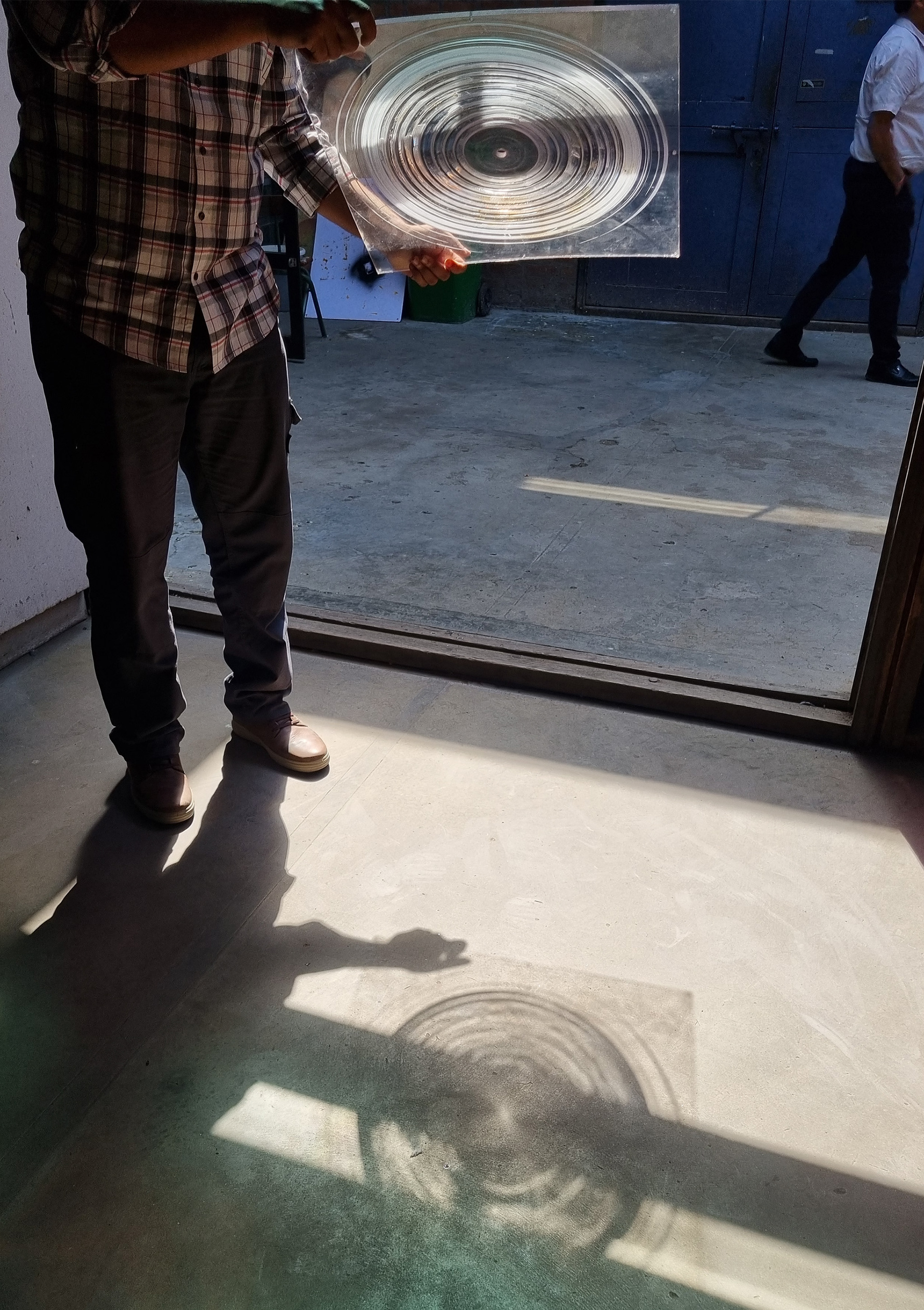
the concept
In the current traditional metal melting process coal is used as a fuel, according the metal melting craftsmen 1kg of cokecoal can melt 200 grams of copper. stating the estimated annual fuel consumption of the Metal casting is around 10-12 tonnes,which costs around 5-6 lakhs in India annually on fuel consumption.
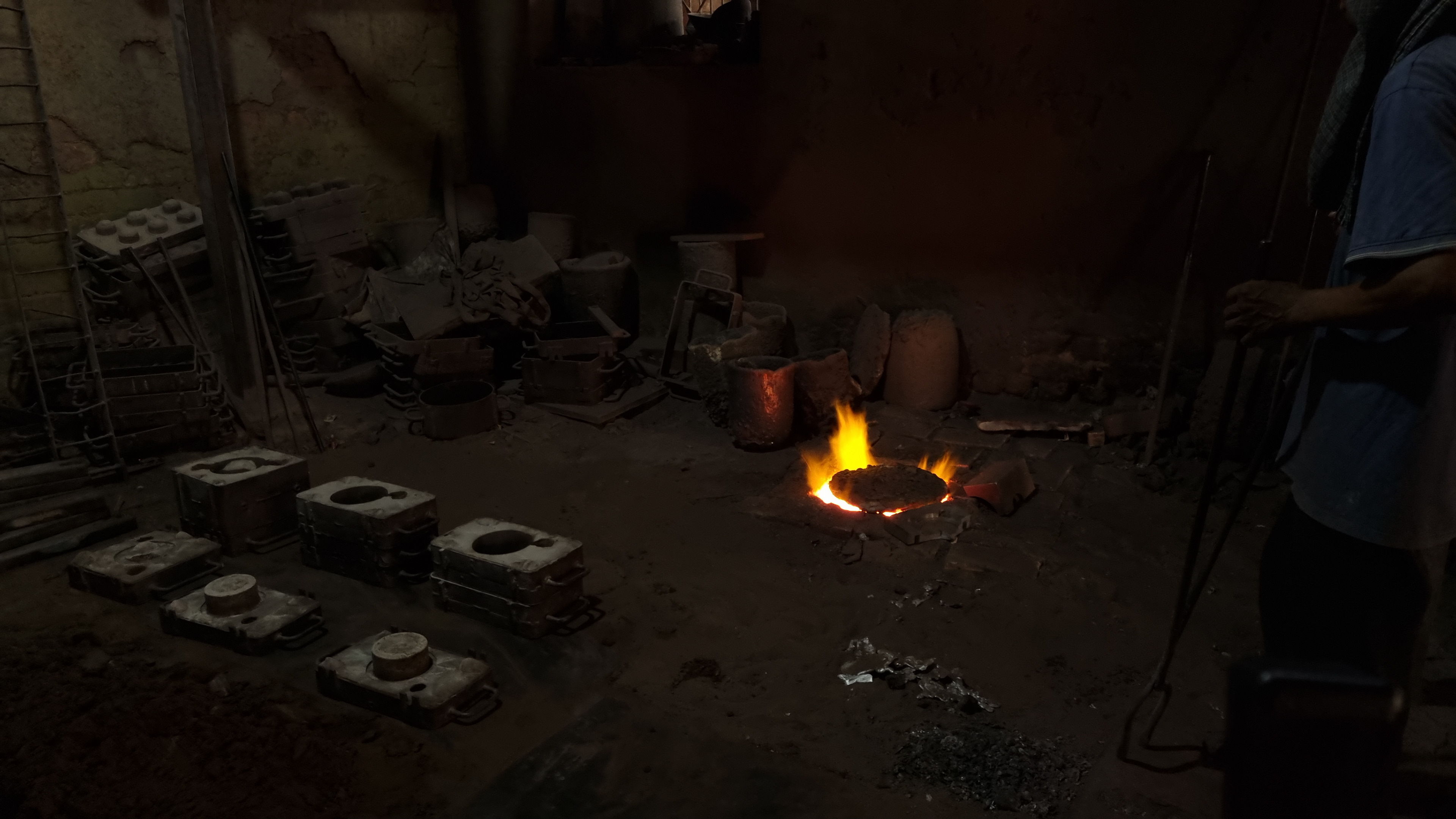
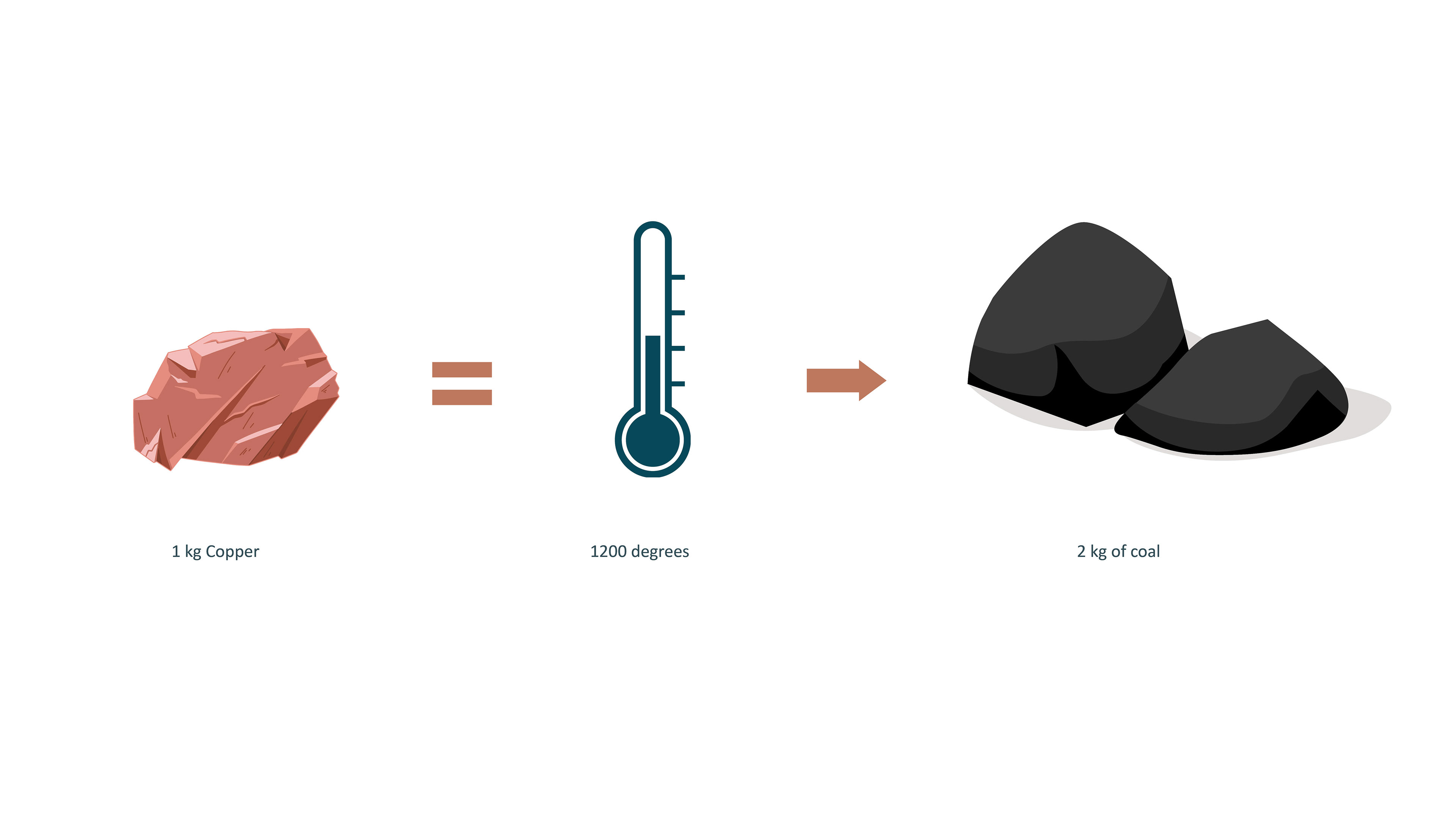
Coal needed to melt 1 kg of Copper
In case of craftsmen using electric furnaces for casting metal in foreground system, the background system still remains heavily on usage of fossil fuels like Coal or electricity generated from them. Where as it become important to find a sustainable solution for metal casting.
Despite the shift from Industrial age to the information age, elements of traditional metalworking systems still exists and put permanent pressure on natural resources, greenhouse gas emissions, air and water pollution, economic growth also affecting the climate change and human health.
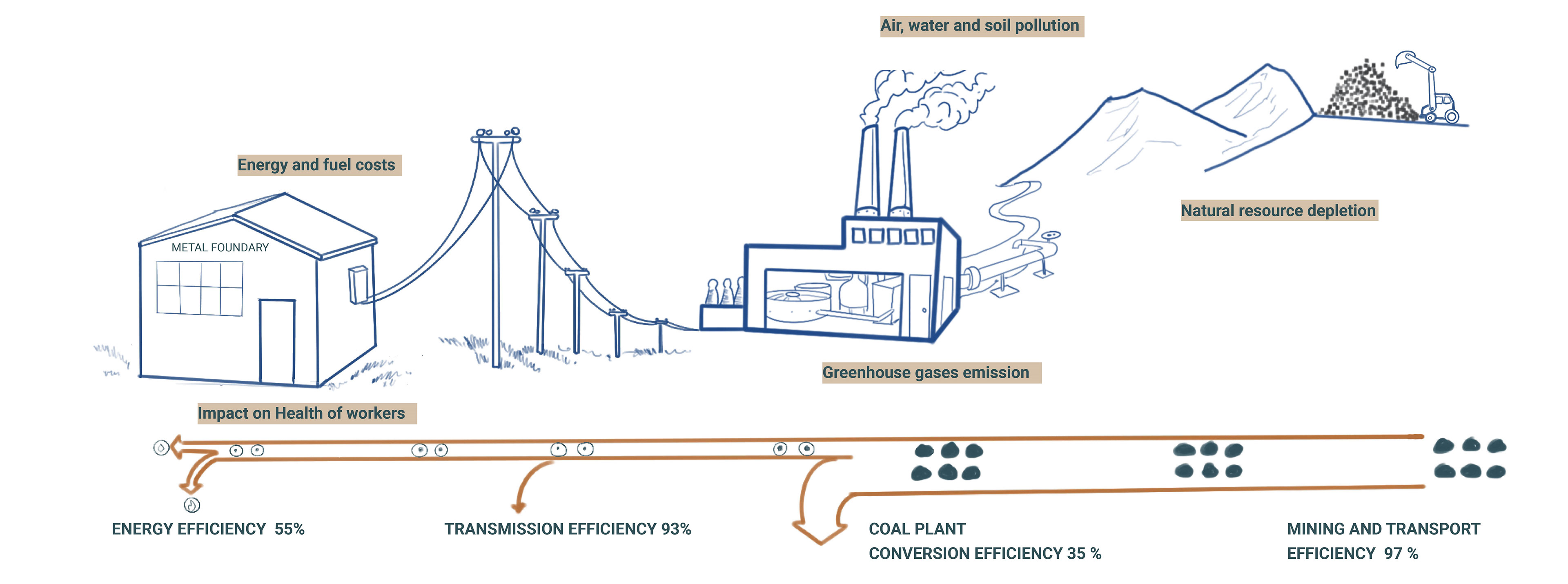
Energy system in metal casting
I came across Luminous Environment Design Strategies, which opened up a new possibility of using Solar Energy by using Fresnel Concentrator, instead of Solar panels, as their efficiency is around 20%. It reminded me of a childhood memory of burning paper with magnifying glass. Fresnel concentrator direct Heat Energy to melt metal, potentially eliminting the need for eletrical furnaces in metal casting.
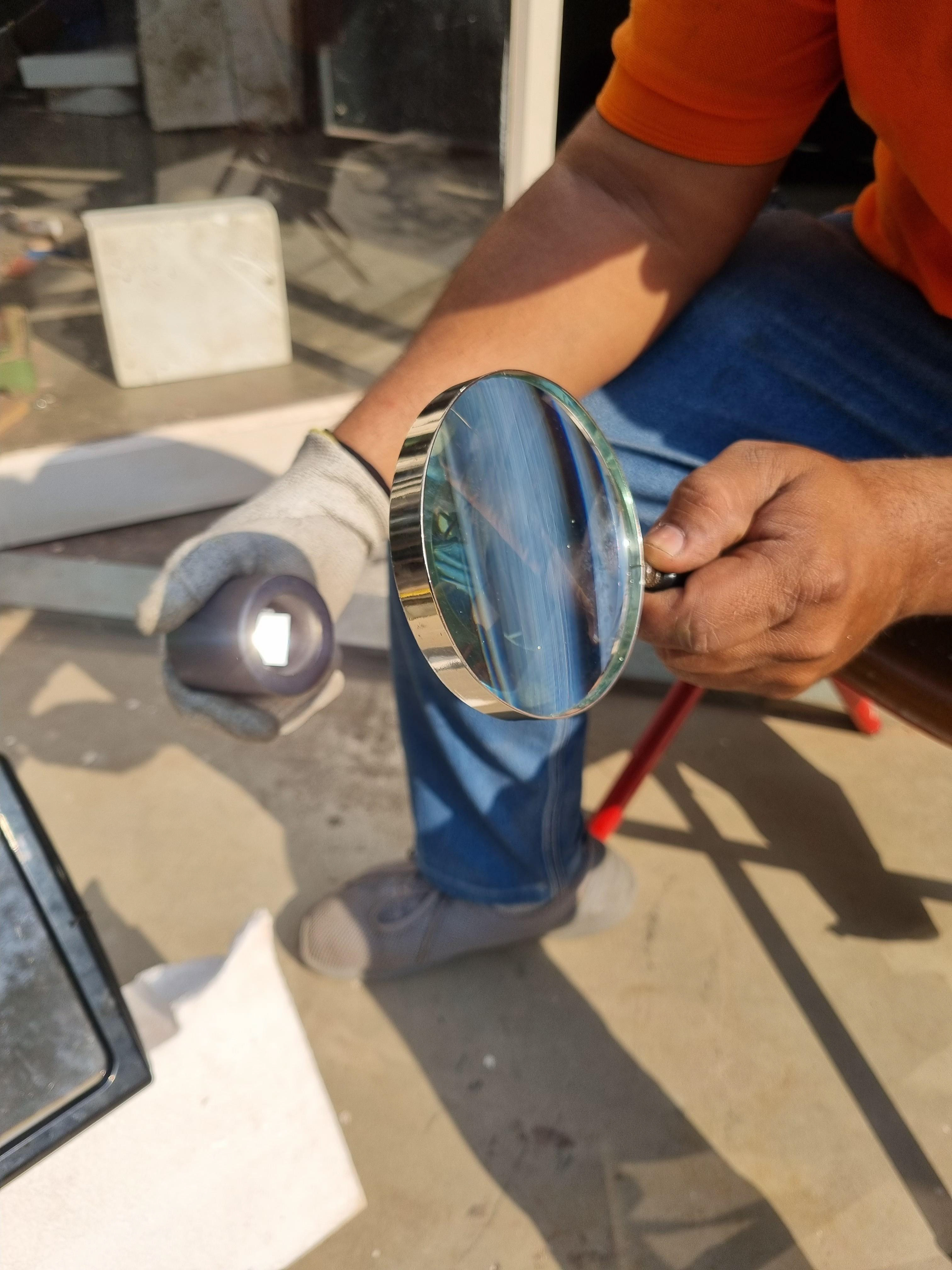
It was an attempt to melt Aluminium .The fresnel lens was set- up, manual handlling the process from 10 am to 3 pm as this time is ideal for capturing sunlight in the crucible. The maximum temperature reached was 233°C. While i couldn't melt the Aluminium, I managed to melt a small amount of soldering wire, which is an alloy of 60% Tin (Sn) and 40% Lead (pb), with a melting point around 230°C.
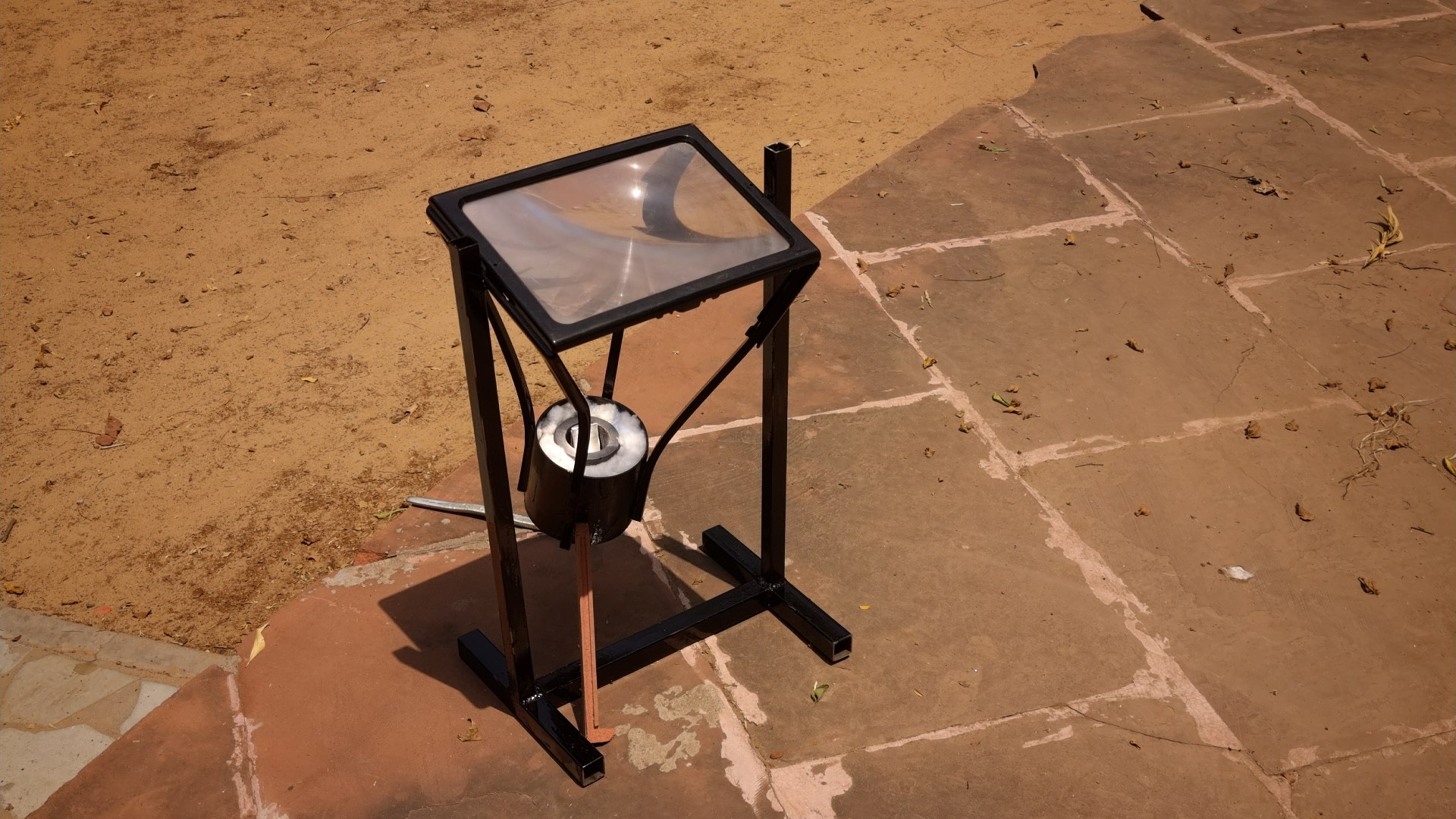
Small prototype made with A4 size 0.8mm Polycarbonate Fresnal Lens
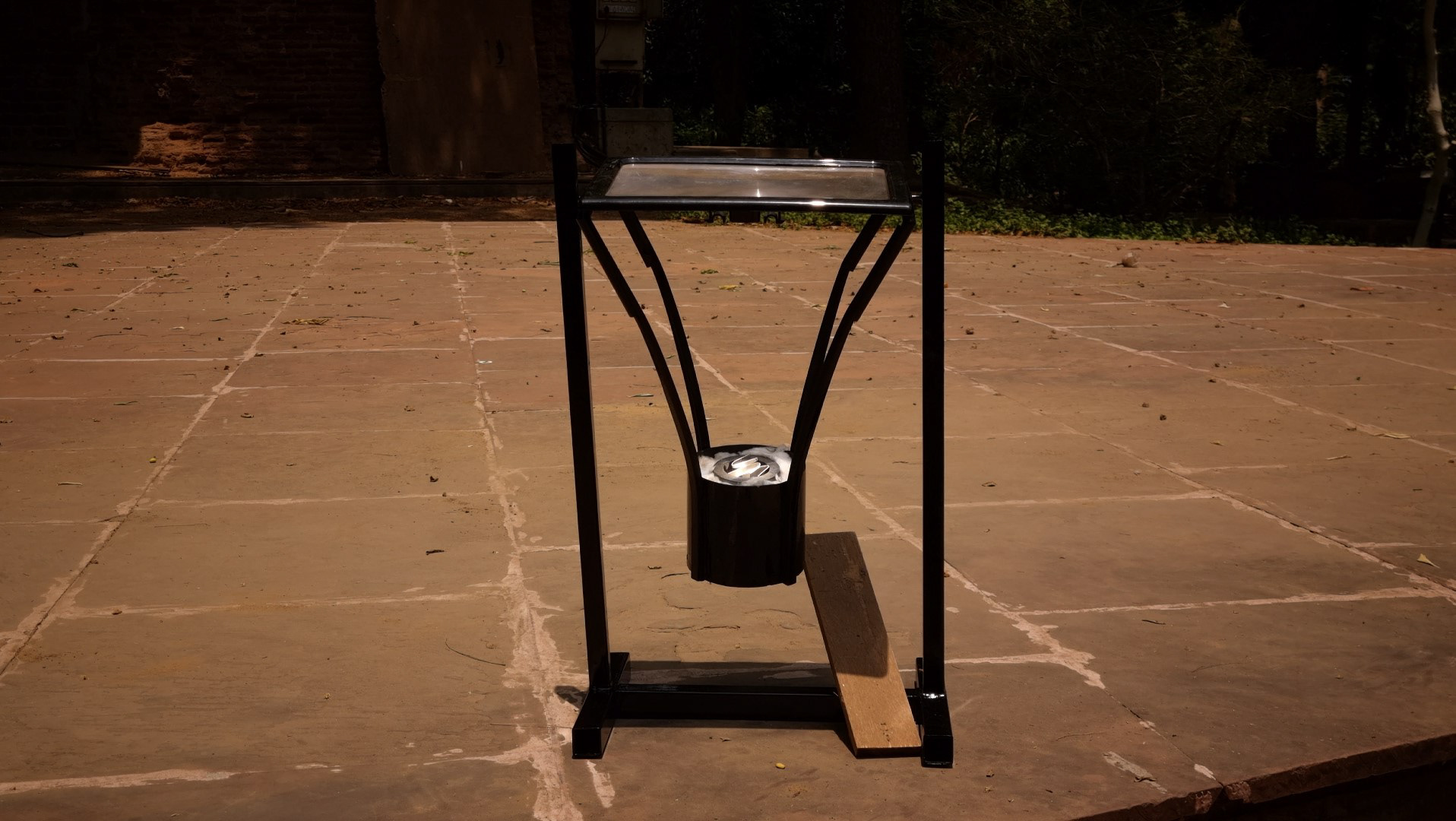
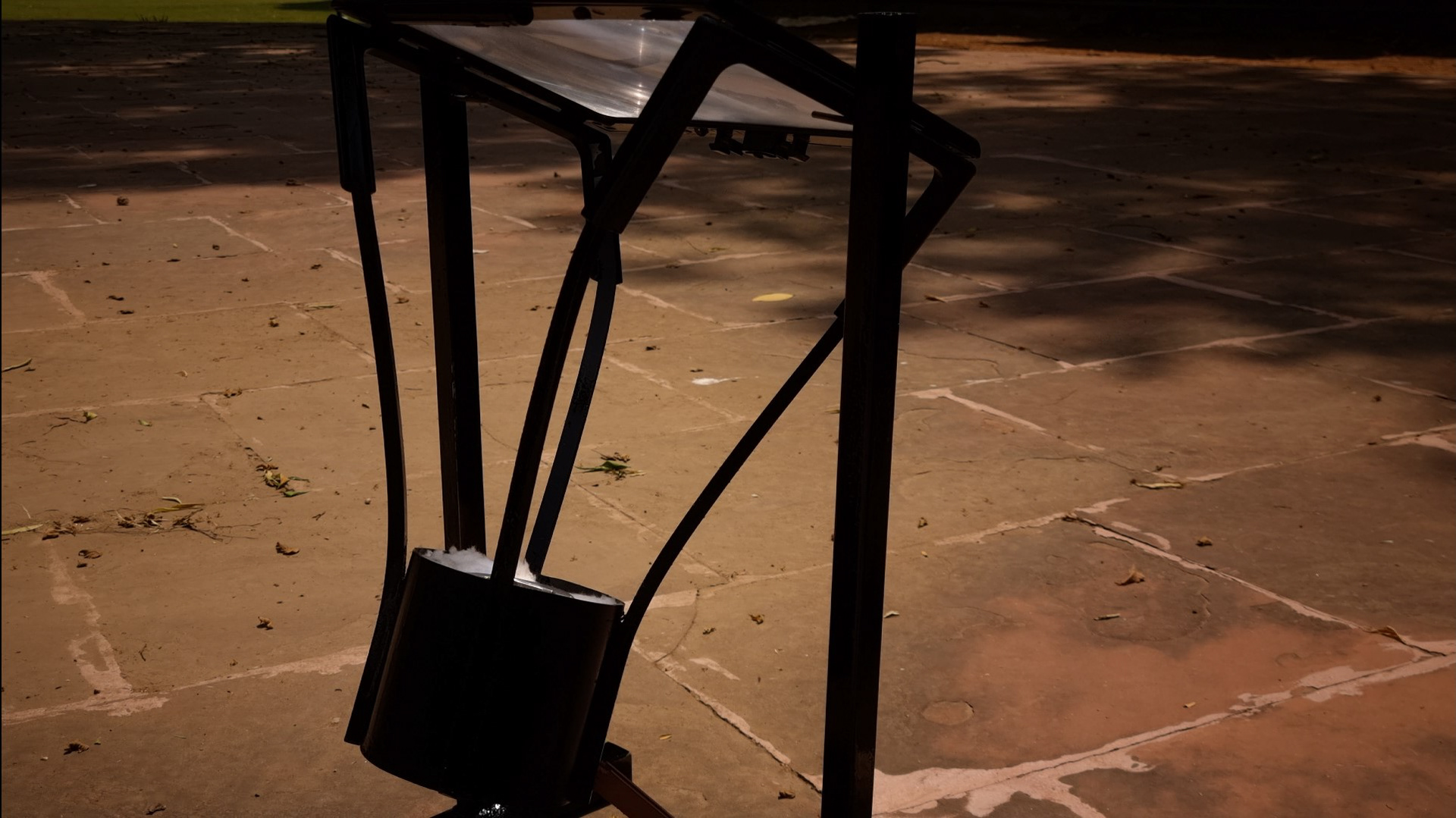
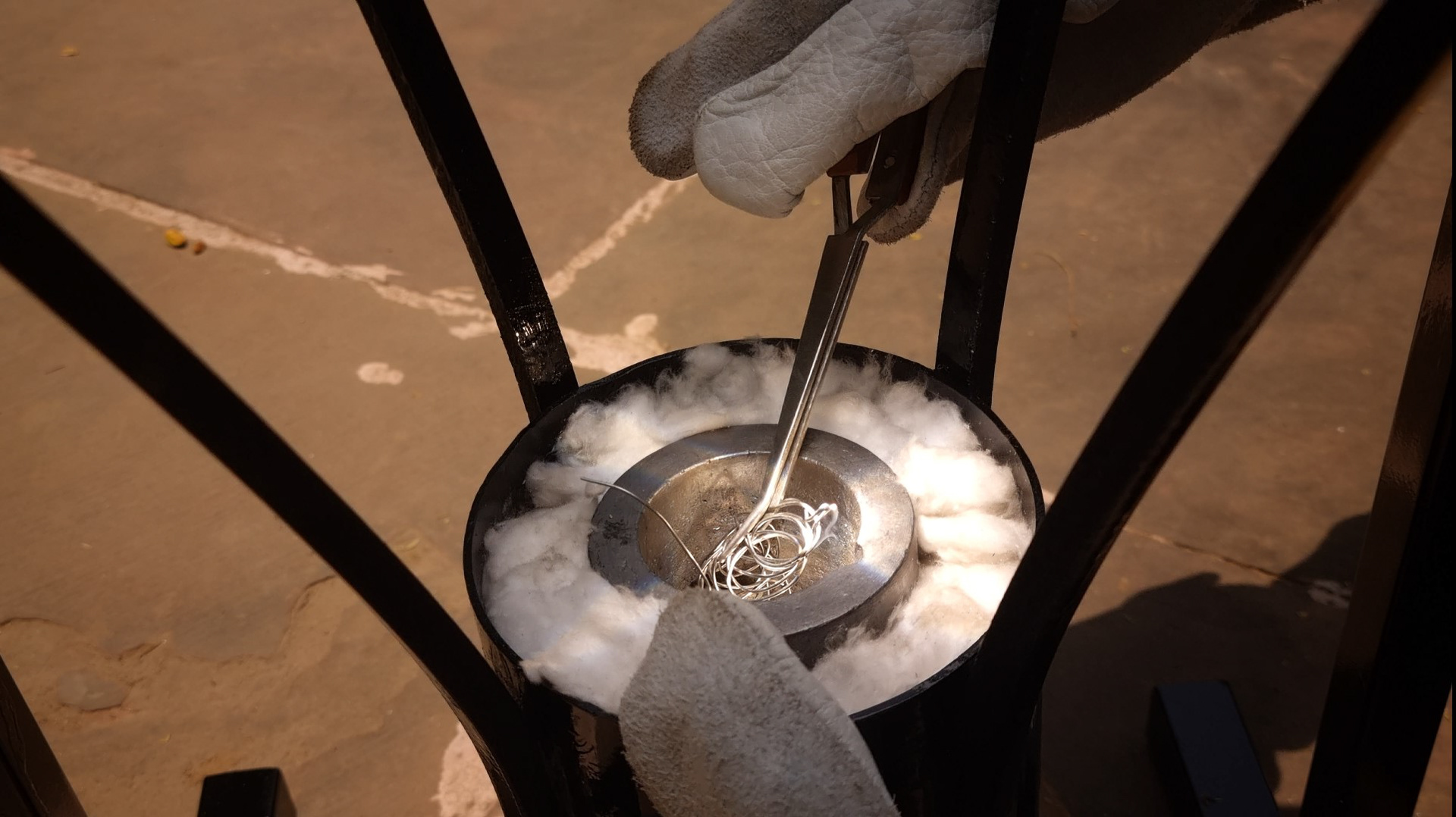
Melting Soldering wire alloy of 60% Tin (Sn) and 40% Lead (pb) when the temperature reached at 230°C.
So to allow temperature for Copper (Cu) Alloys, I need to find a larger Fresnel lens capable of reaching up to 1000°C, there was a need of bigger lens.
the making process
The 8mm Polycarbonate was fixed on Lathe Machine to get proper grooves for Fresnel lens
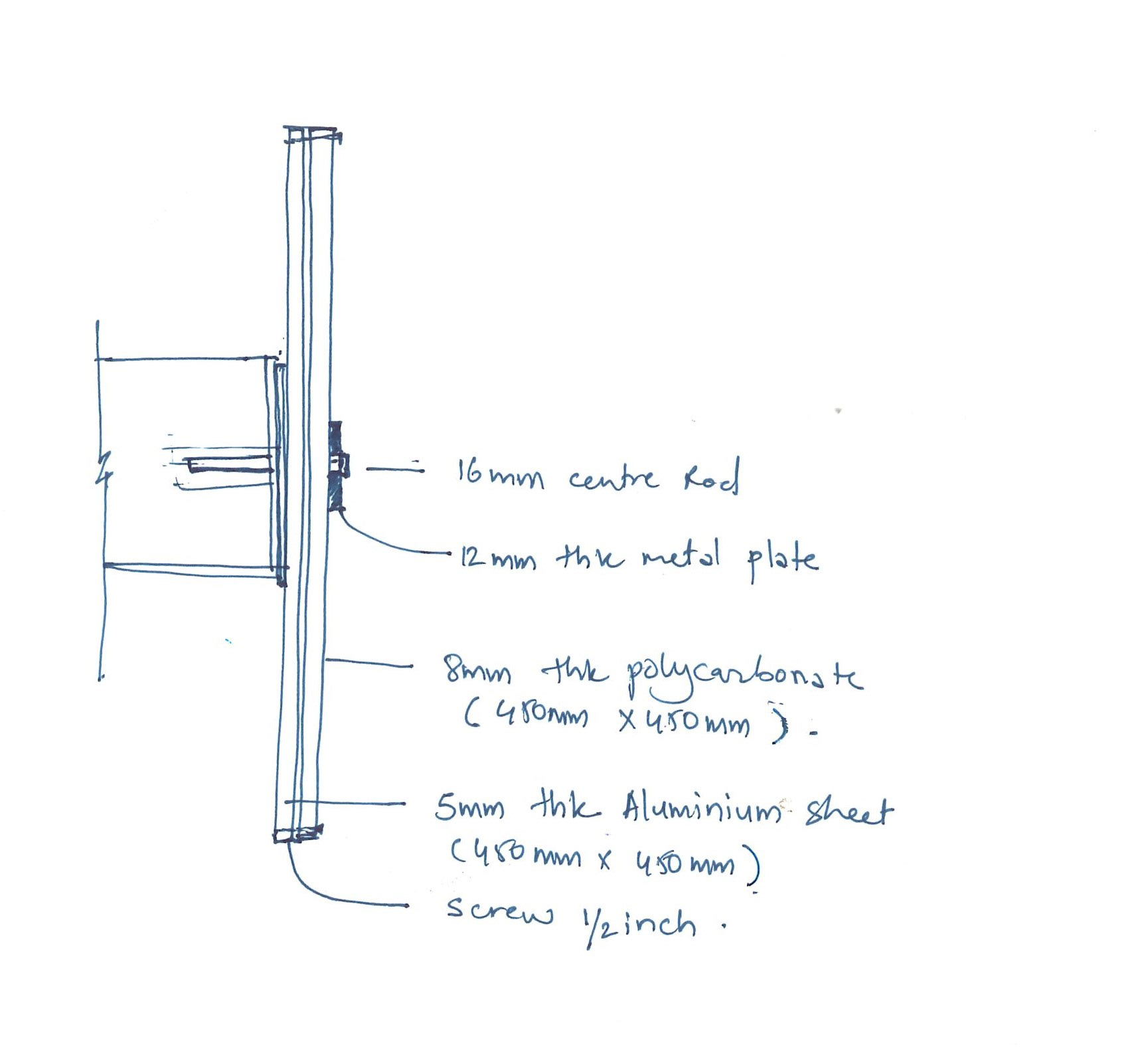
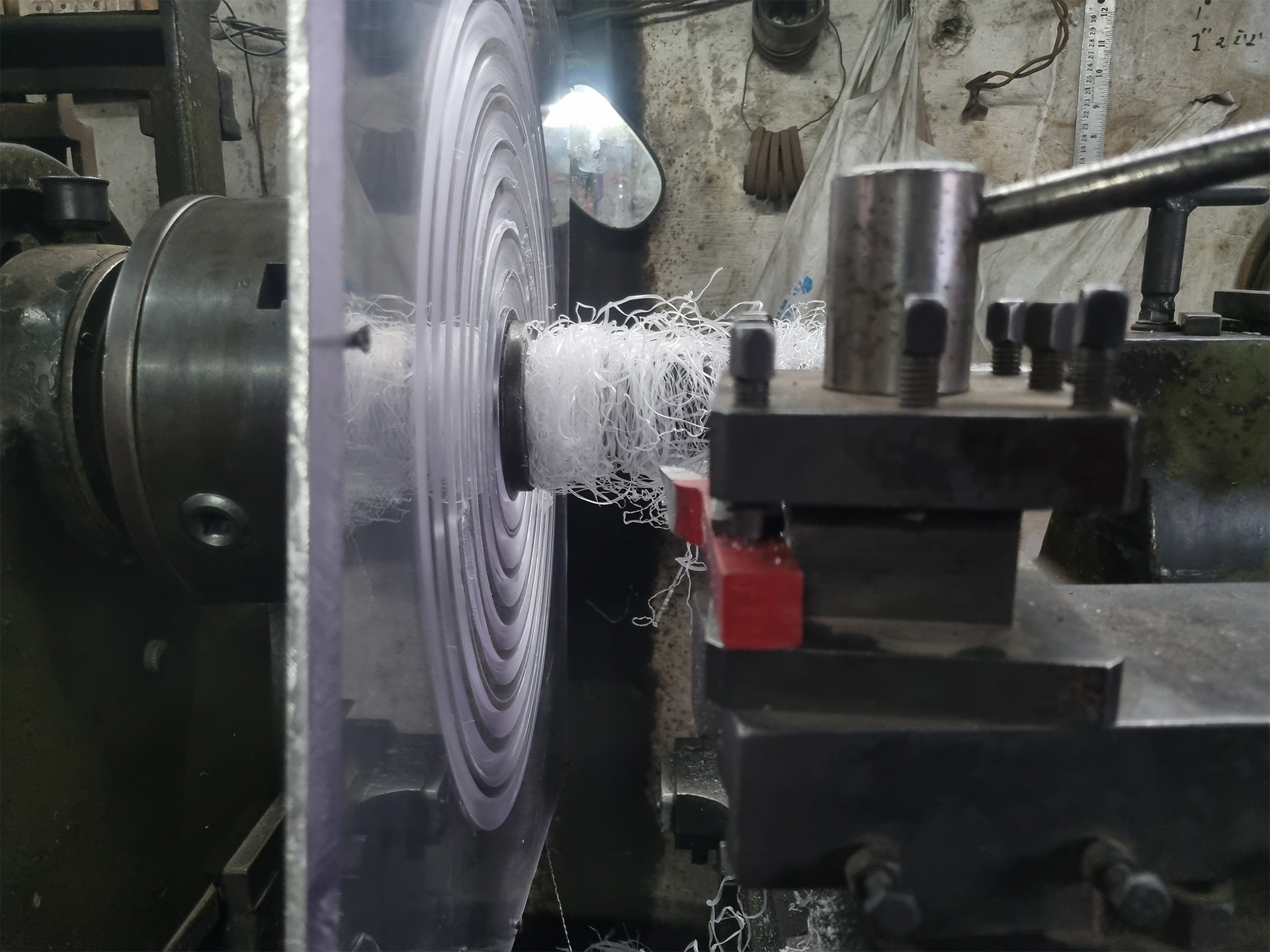
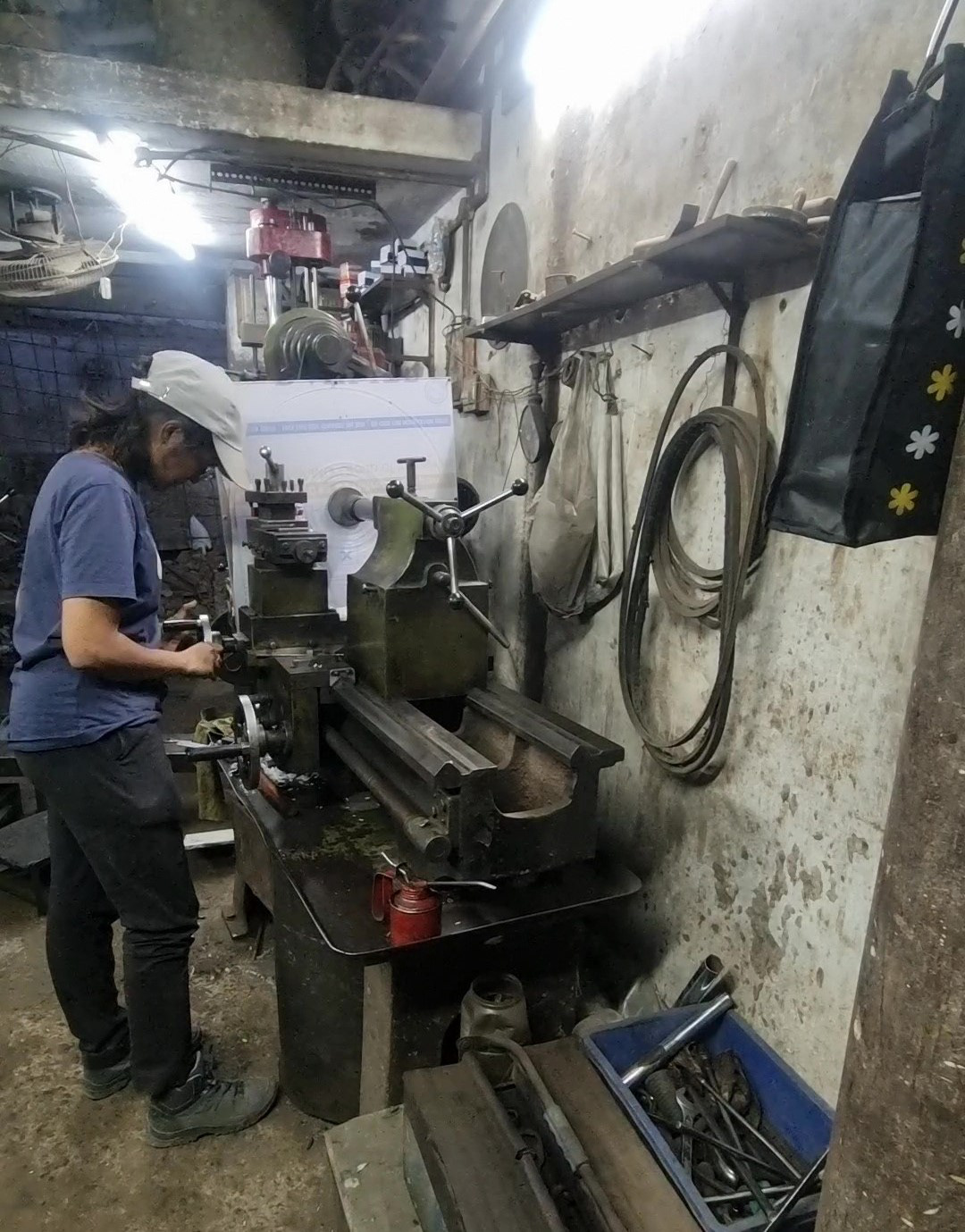
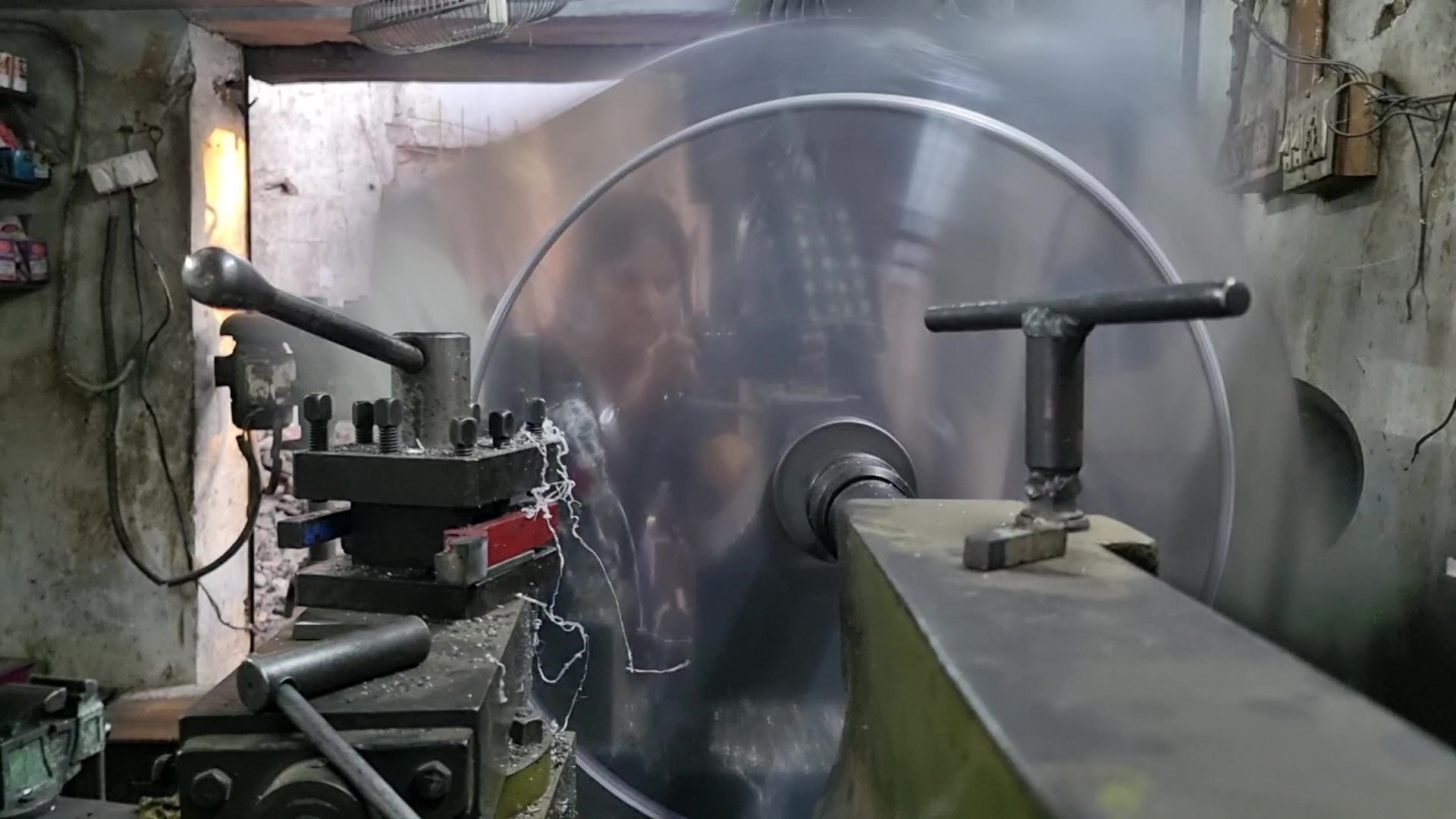
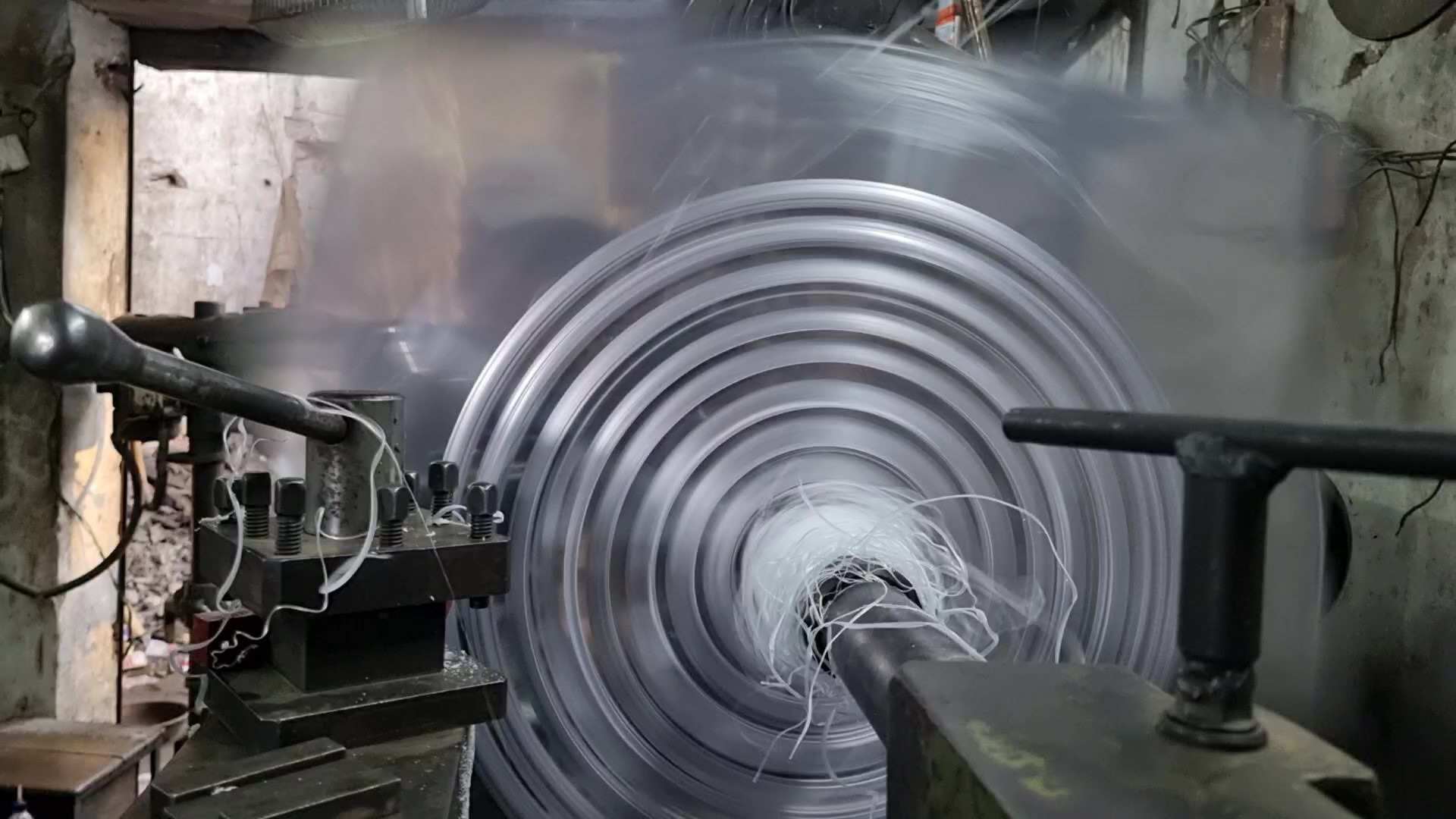
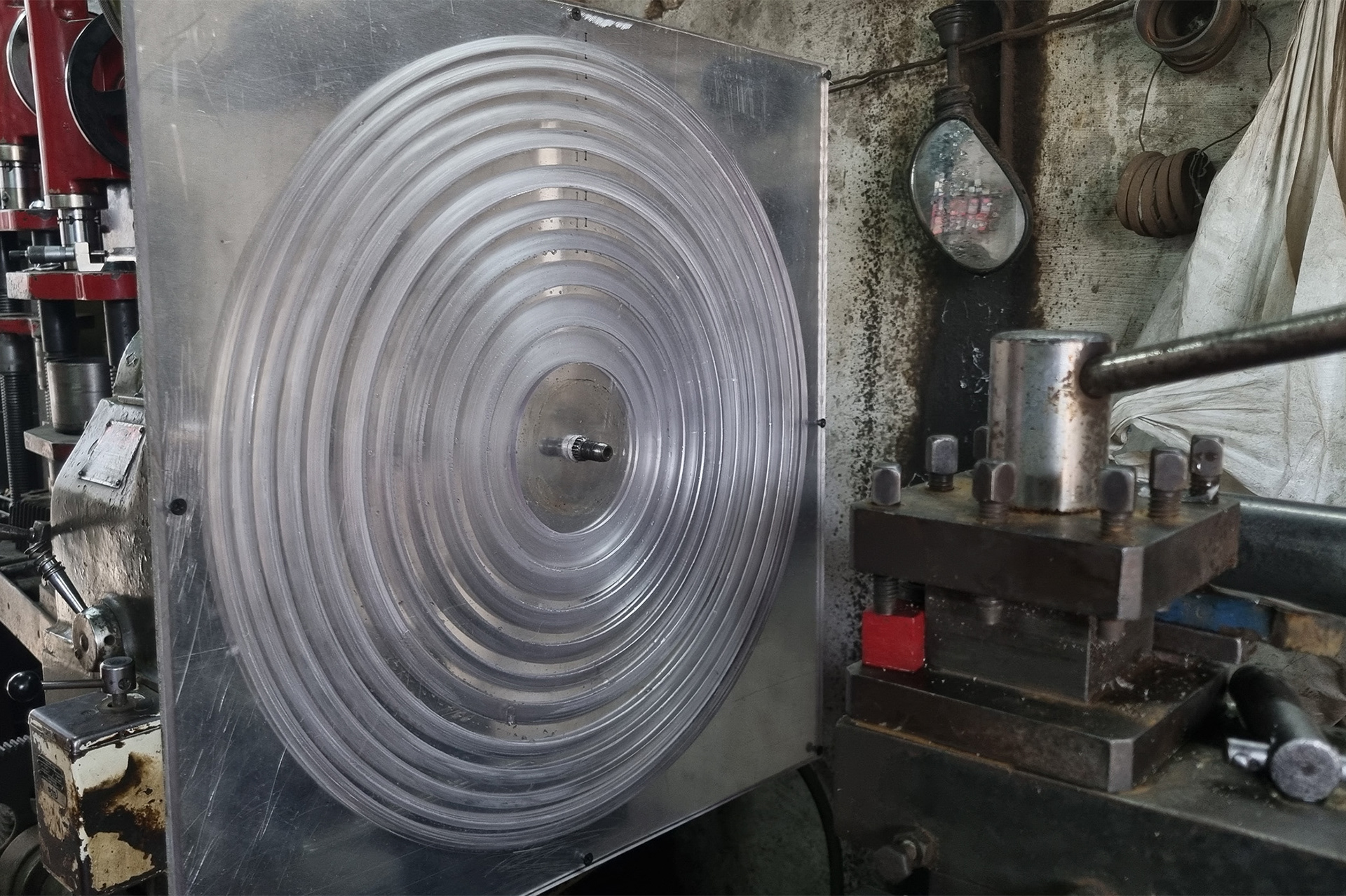